Next-Gen Tesla Electric Car - All You Need To Know | V3Cars
Tesla recently teased 2 new electric cars and confirmed that they will get the next-generation platform with higher efficiencies. Here’s everything Tesla officials announced at the Investor Day event.
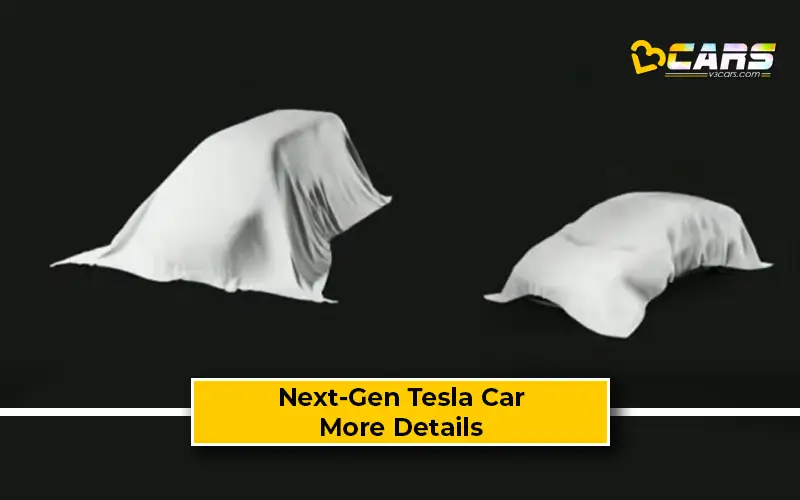
40% Lower Production Footprint
The next-gen electric vehicles from Tesla will come out of the company’s next-generation EV manufacturing plants. Tesla have managed to make efficient use of space and therefore will need a 40% lower area to produce cars at the same pace as before.
50% Reduction In COGS
In terms of cost of goods sold per car, the gains are even bigger at 50%. The cost of goods sold per unit (COGS per unit) is the cost incurred to produce one unit of a product. It includes all the direct costs involved in manufacturing, such as the cost of raw materials, labour and manufacturing overheads.
ZERO Rare Earths
Tesla engineers also announced that they will use proprietary technology to make the permanent magnet motor but with zero rare earths in the new-generation electric cars. Typically, AC induction motors are commonly available without any rare earth minerals. Tesla switched to the more efficient permanent magnet motor in their 2nd gen cars – Model 3 and Model Y.
Now they have found a way to make permanent magnet motors without any rare earth minerals. This will make it easier for them to source raw materials for their next-gen motors while the rest of the automakers scramble to get their hands on rare earths. Their engineering efforts will also help them save $1,000 per unit in manufacturing costs.
100% In-House Controllers
With the use of in-house controllers, Tesla engineers managed to cut the number of chips required in the car. The number of chips not only has a direct impact on the overall cost, it’s also cheaper than a typical silicon for comparable tasks. Using in-house engineered chips also cuts down on their royalties.
Teh Model 3 and Y are in the 50% to 60% range while the Cybertruck will take it up to 85%. Only the next-generation electric cars from Tesla will use 100% in-house chips.
Switch To 48V Architecture
The jump from lead-acid batteries in the Model S and X to lithium packs for low-voltage electricals not only saved them on the weight but also cut down the need for replacement. Now, the jump to 48V architecture in the next-gen vehicle will bring 16% electrical efficiency in the current flow while keeping weight and maintenance costs identical to a 12V lithium battery.
All-new Assembly Process
The biggest change, however, comes in the way they are assembled. Normally, the roof, floor, dashboard and boot bolt on to the frame and then everything else goes in. But that’s not how Elon Musk rolls a Tesla off the production line.
The new process involves attaching the panels to the door separately and attaching the final assembly to the frame. Same goes for the floor, dashboard, boot and rear seats. This process drastically cuts down on the space required to make the car and doesn’t hinder the assembly and roll out of other parts if one of the components requires some fixing.
Since there’s no roof on the car to hinder the assembly of seats, electronics, etc. it also speeds up the process of assembly. It also opens up space for automation with the help of robotics as the robot arms can move around more freely to attach the parts to the panels.
Also Read: MG Comet EV Revealed In India
Pros And Cons Of Electric Vehicles
Note: Check your car’s fuel cost with Fuel Cost Calculator in India
0 Comments
Tesla Cars in India
Model Y
₹59.89 - ₹67.89 lakh*
*Ex-showroom priceUpcoming Tesla Cars
Model X
₹80.00 - ₹95.00 lakh*
*Expected PriceExpected Launch Jun 2026
Model S
₹60.00 - ₹65.00 lakh*
*Expected PriceExpected Launch Jun 2026
Model 3
-
*Expected PriceExpected Launch Oct 2027
Model Y Important Links